Cable Assembly Elements
For medical cable assembly devices and sub-assemblies, we begin with reviewing our customer’s deliverables and requirements. From there, we’ll select the appropriate assembly ‘ingredients’ – the materials and components that meet the products performance, usage, environmental, and aesthetic needs.
Raw Cable Considerations
Conductor Accommodation
Depending on the mechanical and electrical performance requirements of your medical cable assembly, standard stranding, high stranding, or rope-lay configurations may be selected. Common wire constructions may include:
- Tinned Copper
- Tin/Silver Plated Alloy
- Tinsel (Foil lined aramid fiber)
We have capability to process wire gauges down to 38AWG, with micro-wire (>38AWG) capability in-the-works.
We have developed proprietary wire constructions that offer signal and mechanical performance advantages for medical device patient lead-wire applications that demand low triboelectric noise. These wire constructions are available in either copper, alloy or tinsel conductor configurations.
Shielding
EMI and RF interference can degrade signals making diagnosis difficult or even impossible for your medical cable assembly application. Effective shielding can reduce unwanted interference and reduce the amount of active filtering within your medical device.
We can share our knowledge of braided, spiral serve, foil and foil combination shielding, and assist your team in selecting the best one for your application while ensuring shields can properly be terminated and remain effective.
Cable Jacket Materials
We take into consideration appropriate and reliable medical grade, bio-compatible materials for use in cable jacket materials for your medical cable assembly. Considerations such as appearance, flexibility and feel, protection of conductors, durability, cleaning, disinfection and sterilization are taken into account when assisting our customers to select the right cable jacket material. Common jacket materials include:
- Thermoplastic Elastomer –TPE (Santoprene, Versaflex)
- Thermoplastic Urethanes –TPU
- Silicone
- PVC
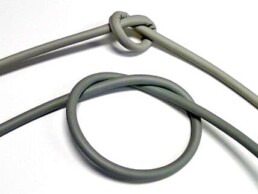
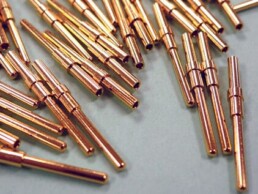
Ensuring your cable assembly makes the right connection
Contact Types
We’ll recommend either solder or crimp style terminations that will be built to relevant IPC-WHMA-610 & 620, J-STD-001 requirements.
Our experience includes:
- Stamped & Rolled Contacts – Open Barrel Pins and Sockets
- Machined Contacts – Closed Barrel Pins and Sockets
- Insulation Displacement Terminations
- Edge Card – Printed Circuit Board Interconnects
Connector Styles
Add additional mechanical strength to your application by molding custom strain reliefs with back-potting to enhance the function and longevity of commercial off-the-shelf (OTS) connectors.
While we consider ourselves to be ‘connector neutral’, you can take advantage of our design team to develop a unique interconnect specific to your application.
- Push/Pull
- Latching/Non-latching
- Magnetic
Suggested blog: Choosing the Right Medical Connectors
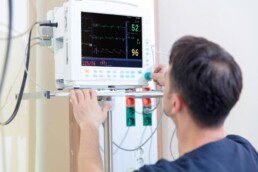
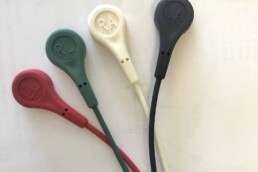
Precision Insert/Over-Molding
The ClearPath Medical manufacturing team has decades of experience with custom molded medical cable assemblies, connectors and other medical interconnect devices. Our OEM partners value our depth of knowledge of part design, mold tool design, mold materials and molding processes.
Over-mold Materials
- Medical Grade Thermoplastic Elastomers (TPE)
- Medical Grade Thermoplastic Urethanes (TPU)
- Medical Grade Polyvinyl Chlorides (PVC)
- Medical Grade Liquid Silicone Rubber (LSR)
Injection Molded Parts
We offer capability to mold rigid components for clamshells, connector nosepieces, backshells and mating receptacles:
- Polycarbonates (PC)
- Polycarbonate/ABS Alloys (PC/ABS)
- ABS
- PBT (Valox)
- Co-polysters
- Delrin
- Nylon
Mold Styles
Depending on the volume and life of your project, we may select to build tooling in either aluminum or full-hardened steel.
Leverage our common base design that can help to reduce time-to-market and tooling NRE expenses. ClearPath Medical has stock tooling to support cable yoke transitions , Electrocardiograph (ECG) Lead Snaps , Touch-Proof DIN 14802-1 & -2 Connectors and more.
Optimal Environmental Performance Considerations
The following table offers guidelines as to the suitability of common cable materials based on various cleaning, disinfection and sterilization methods.
These materials are commonly used for both cable jackets and molded assemblies and will be considered when designing and manufacturing your device.
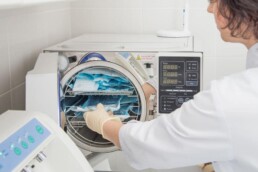
PVC | TPE/TPR | TPU | Silicone | ||
---|---|---|---|---|---|
Cleaning &
Disinfection |
Sodium Hypochlorite (bleach 10%) | Good | Excellent | Poor | Good |
Isopropyl Alcohol | Good | Excellent | Poor | Excellent | |
Glutaral-dehyde (Cidex) | Fair | Excellent | Good | Good | |
Sterilization | Autoclave | Poor | Fair/Good | Poor | Excellent |
Gamma | Excellent | Excellent | Excellent | Excellent | |
Ethylene oxide (ETO) | Excellent | Excellent | Excellent | Good | |
VHP1 (Sterrad) | Good | Good | Good | Excellent | |
Paracetic Acid (Steris) | Good | Good/Excellent | Good | Good/Excellent |
1Vaporized Hydrogen Peroxide
We always ensure compliance to RoHS and REACH directives.
We support a number of validation tests in house, including:
Flex Cycle Testing
Tensile Load Testing
Compression Load Testing
Mate and Un-mate Cycle testing
Chemical Withstand
(This relates to design and test for cleaning solutions: 10% bleach, 2% glutaraldehyde such as Cidex, 70 & 90% IPA, and other commonly used hospital disinfectants.)
Voltage Testing – up to 10kV dielectric withstand
Requirement-based Design and Testing
Your products will be designed and tested to meet the following specifications depending on your design project; IEC 60601 requirements for medical equipment and accessories, ANSI AAMI EC53 for ECG Leadsets and Cables and ISO-10993 for biocompatibility.